Pumping concrete is a fast, flexible, and efficient placement method which has grown in use along with the capabilities of pumping equipment and the skills of pumping contractors.
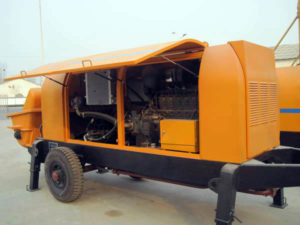
In a concrete pump line, concrete moves in the form of a cylinder or slug separated from the pump line wall by a lubricating layer of water, cement, and fine sand. To keep moving through the line, the mix must be dense, cohesive, and have sufficient mortar. When concrete is pumped, if spaces or voids between aggregates are not filled with mortar, or if the mortar is too thin and runny, pump pressures cause segregation, forcing water through the mix. When this happens, the lubricating layer is lost, causing coarse particles interlock, friction to increase, and the concrete to stop moving. To prevent plugs, the pressure at which segregation occurs must be greater than the pressure needed to pump the concrete. This can be accomplished by filling the spaces between aggregate particles with smaller aggregate.
The properties of coarse aggregates that affect pumpability are maximum size, shape and surface texture, porosity, and gradation. Generally, the line diameter must be 3.5 to 4 times greater than the maximum aggregate size. Shape and surface texture are important because concretes made with angular, rough particles usually have to have a high mortar content to be pumpable. For best pumpability, coarse aggregate grading should fall in the center of the gradation specifications. Porosity will affect pumpability if a significant amount of mix water is absorbed by the aggregate during pumping. When absorption causes problems, one solution is to thoroughly wet the aggregate stockpiles before batching the concrete.