In the production process of concrete, concrete batching plants use a great deal of water. Much wast water is produced in cleaning of mixing devices and delivery vehicles. This not only increases consumption speed of valuable water but also does enormous harm to environment. To solve the problem experts have invented waste water treatment system which recycles waste water completely. The system includes waste water discharging groove, sand separator, waste water settling tank, stirrer, clarification tank, conveying pump and filter press etc.
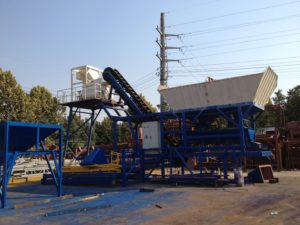
Normally the WWT system for concrete batching plants contain four waste water tanks and three tanks for clarification. Each of the four tanks is equipped with fence and stirrer. The first three have slurry pump in them as well. Both the second and fourth tanks have a level meter. Special pump for waste water is applied in each of the three settling tanks. The stirrers work regularly in order to keep evenness of the water quality. In the system the tanks must be arranged in given orders, because each tank serves as precondition for the following one. The tanks connect with each other through flow pipes at the bottom and through pumps at the top. Whenever a tank is in shortage of water, pumps can be started to supplement water into it. In case of excessive amount of water, the extra water will flows back into the previous tank. At the concrete batching plant site water flowing grooves are connected to waste water tanks. This makes it more convenient to keep the site dry by collecting rain water efficiently. Further more, it reduces operation cost by avoiding water collecting and pumping using machines. Specialized water flow grooves are constructed by the plant as well as vehicle cleaning system. In this way wast water gathers into the tanks for centralized treatment.