For construction projects to ensure the quality of high-quality concrete is fundamental, but a lot of concrete mixing station due to low factory automation equipment weighing accuracy, making stirring ingredients large deviations, and ultimately affect the quality of the project. To this end haomei company by introducing foreign advanced technology of automatic batching, and with IPC technology completely solves the problem of concrete mixing station batching accuracy.
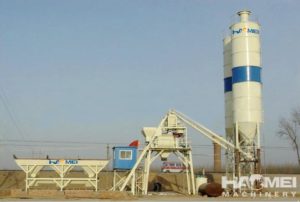
We solved the three main aspects:
1, to solve a variety of raw materials were weighed accurately problem;
2, the solution to control the speed of conveyor belt material;
3, to solve the motor start and stop control ingredients;
A, electrical control system uses ” control computer + display instrument,” the control module sets, is a multi-tasking, high intelligence, high stability of the automatic control system, the key electrical components are imported, install the operating room with the host platform on the same plane, in order to facilitate the control of observation. The entire system executed by the strong electric devices, fault detection device, the control unit module controller 2003 with scales, industrial control computer, control of several major components, such as management package. Industrial control machines without built-in input and output cards and data acquisition card. Each bar corresponds to a display instrument Road, completed the scale value display instrument displays, industrial control computer determines the output signal based on the signal state, in order to control each instrument, the purpose of the automatic control of production.
The basic composition of the stationary concrete batching plant entire system.
B, in the system, each weighing a BR2003 by the instrumentation and sensors, each scale independent, mutual non-interference. When the system work through BR2007 instrument (or computer) each piece BR2003 instrument commands (such as metering, discharge, etc.) and distributed execution time lag meter BR2003 comes up the timing of the whole system work, each detection by the mixing station point into the BR2007 instruments, through the implementation of the instrument to judge each BR2003 production batches in order to achieve automatic. BR2007 meter will each actual value of each ingredient BR2003 instrument into the computer, by JK-W software will save the data recorded by a random time, after the composition of the various software processing and report output.
C, depending on the grade of concrete production, process and feed the material to adjust the feed timing may be such as to meet the cast sand, cement, admixture, fly ash in the mixer and stirred for a certain time after the second feed of the stone cast process 80% of the first vote and water, stirring for some time before the remainder of the cast of secondary drowning process. Feeding sequence and timing of each feed material can set the software to facilitate debugging.
System is simple and intuitive, good anti-jamming performance, easy to maintain, easy to expand, high material ratio control accuracy. There are more perfect production report output generation selection output, using intelligent software calibration scales, calibration simple connection gravel Moisture Meter to automatically compensate for increased online sand water reduction, the system has various fault alarm function, and can prompt failure exclusion method. System reserved network interface, network access management.