A concrete batching plant is where various materials are mixed with an aim of creating concrete. Some of these materials include sand, lime, water, gravel, fly ash and cement. The following are various parts of a concrete batching plant:
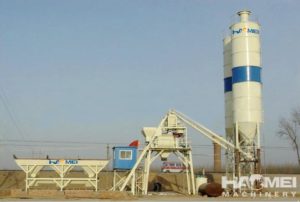
· Mixers
· Heating or Cooling units
· Dust collectors
· Cement silos
· Cement Mixer (In case of a wet batching plant)
· Radial stackers
· Aggregate batchers
· Batch plant control
Concrete plant is totally run by an operator who uses a computer to input the required measurements of concrete. After pressing the start button, different measurements of inputs are transported into the mixer. The resulting mix is released into a transport trunk and it’s finally transported to a construction site.
There are three types of mixers namely tilt, twin shaft and pan. A twin shaft will provide an even consistency of the concrete while ensuring a large production. On the other hand, a tilt mixer ensures a consistency mix with less labor and costs. Compared to twin shaft mixer, a tilt mixer doesn’t provide a large output.Well, the following is a guide on how a concrete batching plants works:Raw materials are first poured into large containers and they are delivered into a central mixer via a conveyor built. The materials are precisely weighed before being transported to the mixer thereby maintaining consistency in output. Concrete batching plants can be categorized into 4 major parts namely powder feeding, aggregate feeding, storage and conveyance. Concrete batching plants are normally used to make quaking concrete and hard concrete suitable for bridge and road construction. When control system of a mixer is directly connected to a source of electricity, system initialization will take place which includes concrete slump, productivity, formula number and concrete grade. Each and every container is tested according to weighing system. Belt conveyor is then started with an aim of transmitting aggregate to the hopper. Cement tank and fly ash valve on the other hand should be opened in order to make the admixture flow into the hopper. The door of the hopper is automatically opened when the total weight of materials reaches a specific amount. When the time set is over, the door to the concrete mixer will open and concrete will flow into the mixer truck. The process should be done very carefully in order to avoid contamination of concrete.
Experts always suggest that proper planning should be done under export supervision before at concrete batching plant is ordered onto a manufacturer. Following factors should be kept in mind while designing of a batching plant:
1. Land availability.
2. Distance of the plant from raw materials like aggregates, cement, sand, water and chemicals.
3. Distance of the plant from a major construction sites since the concrete has to be delivered eventually to those places.
4. Availability of trained personnel to run the plant efficiently.
If you are planning to purchase a batching plant, you are recommended to have it near your construction sites in order to save on time. If any question, feel free to contact a support team for help from accredited manufacturers.
It’s very important to engage concrete batching plant manufacturers from Europe or USA since it has been seen that the saving of your dollars by buying cheap imitation machines from China has cost a lot of money and reputation at many project sites around the world.
It’s also very important to order the plant according to your specific requirements of concrete. One should be very specific about the requirement of mixer that come in several configurations for specific uses like that of ready-mix , precast and at the specific applications. One should also consider what types of raw materials locally so that Products can be made accordingly.