batching plant work flow: a concrete mixer control system startup into man machine dialogue interface, system initialization, including recipe, grade of concrete, slump, production amount. According to the sensor on each silo, the metering hopper detection, full signal output empty material or material, suggesting that operation personnel determine whether to start mixing control program. Start the sand, stone belt motor into the expected aggregate weighing hopper; open the fly ash, cement silo butterfly valve, start the motor of screw conveyor conveying fly ash and cement to powder weighing bucket; open water pump and the admixture of additives and water flows into a measuring bucket. Metering meet the requirements of the measurement after the bucket Doumen, ingredients into the mixer, stirring, to set the time to open the concrete mixer door, concrete into the concrete mixer truck.
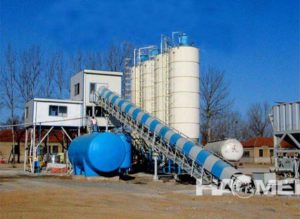
The concrete batching plant consists of 5 main systems, such as concrete mixer, material weighing system, material conveying system, material storage system and control system, etc..
1, concrete mixer,: mixer according to their mixing mode divided into forced mixer and self – falling mixer. The forced mixer is the mainstream of concrete batching plant at home and abroad, it can stir the flow, semi dry and hard and so on many concrete. The self – falling mixer mainly stirs the mobile concrete plant and is seldom used in the batching plant.. Compulsory mixer in the form of the structure as the main planetary mixer, single horizontal shaft mixer and twin shaft mixer. The comprehensive performance especially in the twin shaft compulsory mixer best. Our series of concrete mixing plant all adopt double horizontal shaft forced mixer.
2. Material weighing system: material weighing system is the key part which affects the concrete quality and the concrete production cost. It is divided into three parts: aggregate weighing, powder weighing and liquid weighing.. Under normal circumstances, per hour 35 cubic meters of concrete batching plant using superposition weighing mode, namely aggregate (sand, stone) with a pair of scales, cement and fly ash with a pair of scales, water and liquid additive weighing respectively, then liquid additive put into water, said Dou pre mixed. In the concrete batching plant of 50 cubic meters per hour, the weight of each material is independently weighed and the electronic scale and microcomputer control are used.. Aggregate weighing accuracy is less than 2%, cement, powder, water and additive weighing accuracy reached less than 1%.
3. material conveying system: material conveying by the aggregate transportation, powder conveying, water and admixture transportation three parts. At present, there are two ways of feeding the concrete batching plant in the aggregate conveying hopper conveyer and belt conveyer.. The advantages of the hopper lifting is small area, simple structure. The advantage of belt transportation is that the transportation distance, the efficiency and the failure rate are high.. Belt conveyor is mainly applied to aggregate temporary storage of the concrete batching plant, so as to improve the productivity of mixing plant. Powder for concrete is mainly cement, fly ash and slag. At present, the screw conveyer is generally used in the mixing plant .. The advantages of screw transport are simple structure, low cost and reliable use.. Water and liquid additives were transported by the pump respectively.
4. material storage system: the concrete mixing plant used in the same way of storage of materials. Aggregate piled up in the open air (also have large urban commercial concrete batching plant closed silo); powder with cement silo storage; admixture with steel structure container storage.
5. Control system: the control system of the batching plant is the central nerve of the whole equipment.. Control system according to the requirements of different users and stirring station size and different function and preparation, general construction site with small concrete batching plant control system simple, and large batching plant system is relatively complicated.