Cracked concrete can happen for lots of reasons. Could be a bad mix design for the intended use, could be due to material or ambient weather conditions, could be lots of things, but could it be because of the concrete plant? Of course, a concrete plant can and does make bad concrete, but most concrete plants have a system in place to catch a bad batch.
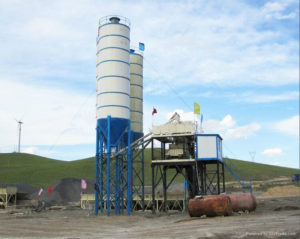
A concrete plant can make a bad batch for lots of reasons. Maybe a gate or valve got stuck or material that was supposed to end up in a mixer ended up overflowing or not getting into the mixer. Anytime the desired amount of each material is not put into the mixer, the batch could be considered bad. Most concrete plants today are equipped with ticket printers attached to the scales and meters on the plant, and most concrete plants provide a printed ticket of the materials when the load of concrete is delivered. When a load of concrete is batched and does not meet the specifications of what is ordered, the concrete plant operator will normally dispose of the concrete and batch a new load.
Now are some other variables. Most concrete mixer trucks have water on board, and most concrete finishers prefer to finish wet concrete. It is no uncommon for a truck driver to add water to the mix. Normally this is because the contractor has requested more water, but different drivers do different things. It is also possible that a concrete plant operator saw the concrete was outside of what was expected and sent the load with the ticked putting the responsibility of finding the load of material is wrong on the contractor.
Most frequently, concrete cracking is caused because the mix design used wasn’t designed specifically for what it is being used for. Concrete plants across the country take calls daily for 3500 psi mix, or foundation mix or similar. In reality there can be lots of differences in a 3500 psi mix. Mix designers can make concrete do amazing things and one mix does not suit all.